succesvolle case
Project Germany
project tijd: 2012
klant hoofdproducten: Final batch rubber (rubber afdichtingen), een van de grootste fabrikanten pijpafdichting in Europa
Xinda machine: 3-flight co-kneedinrichting SJW-200
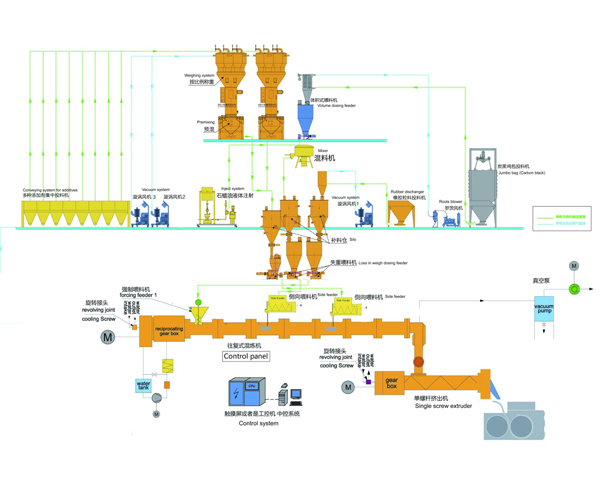
Introductie van het project
1. In 2011 heeft de klant het nieuwe productieproces van hun producten met Xinda besproken, en beide partijen vast te stellen om samen te werken in R & D. Tijdens deze periode, gecorrigeerd ze het productieproces in Xinda laboratorium voor vele malen en nam het terug naar Duitsland herhaalde proeven. De kwaliteit van het eindproduct hoger dan het origineel.
2.In 2012, the customer purchased xinda co-kneader SJW-200 to produce final batch rubber for rubber seal products, changing the processing technology of traditional banbury kneaders and milling rollers, which greatly improved the stability of product performance. At the same time, high degree of automation of Co-kneader improved the workshop production environment. The capacity per unit compounding line can reach 10,000 tons/year.
Terugkoppeling en beoordelen van de Klant
1. Lage afschuiving en hoge dispersie is de unieke eigenschap van Co-kneder. Grondstoffen, zoals rubberdeeltjes, carbon black, witte olie, rubber versneller en hardingsmiddel en dergelijke, voert achtereenvolgens op het zuigermachine in secties, met nauwkeurige materiaal temperatuurregeling voldoende dispersie en mengen uitstekende productprestaties en goede producthomogeniteit en stabiliteit.
2. Mate van automatisering van Co-kneder in productie is extreem hoog. Grondstoffen kunnen worden onderverdeeld in groepen en afgemeten in doorsneden gravimetrisch voersysteem. De rubberdeeltjes, carbon black, witte olie en vulcanisatiemiddel worden toegevoerd in een gesloten wijze. Dus de workshop productie-omgeving is heel schoon.
3.Three-flight Co-kneder SJW-200 heeft een hoge productiecapaciteit en een laag energieverbruik. Vergeleken met de traditionele interne raffinage plus geopend raffinage productie-apparatuur, is het energieverbruik per ton verminderd met 20% - 30%.
4. De bovenste fase zuigermachine neemt een clamshell vatting, terwijl schroef van de tweede trap pelletiseren extruder kunnen worden gescheiden door terugtrekken. Wanneer derhalve formules wijzigen of het apparaat onderhoud nodig heeft, kan snel worden geopend en gereinigd, wat de tijd van conversie en onderhoud verkort.
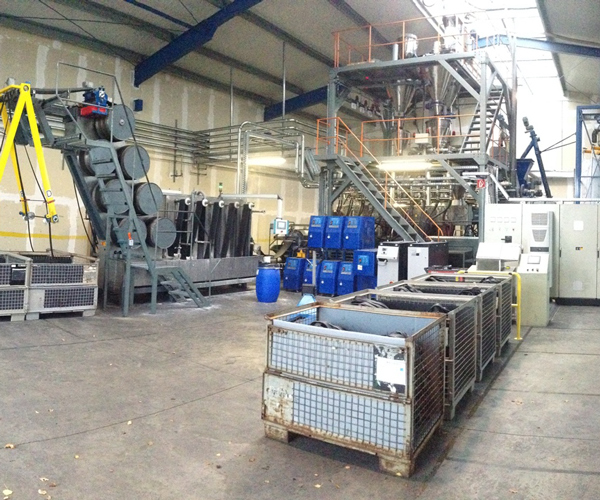
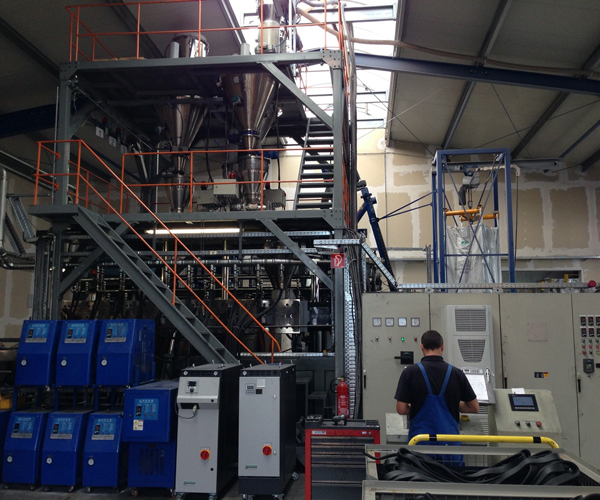